Why Choosing the Right Custom Nut Manufacturer is Crucial for Your Industry Success
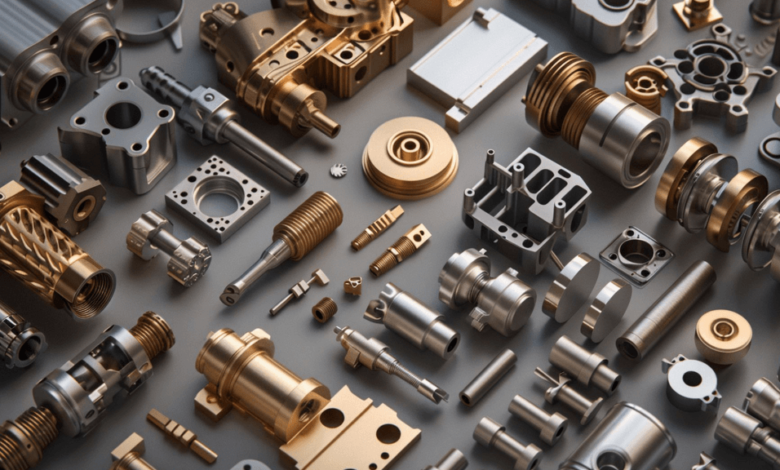
In industries ranging from aerospace to automotive, construction to electronics, fastening components like nuts are indispensable. While standard nuts suffice for many applications, the increasing complexity of modern machinery and infrastructure demands specialized solutions. This is where a custom nut manufacturer becomes a vital partner—designing and producing nuts tailored precisely to the needs of unique projects and environments.
This article dives deep into the role of a custom nut manufacturer, the benefits of working with one, the manufacturing process, and how to select a reliable partner for your fastening needs.
Understanding the Role of a Custom Nut Manufacturer
A custom nut manufacturer specializes in producing nuts that deviate from standard catalog specifications to meet exact client requirements. These custom nuts may feature:
- Unique thread sizes, pitches, or profiles
- Special materials suited for specific mechanical or environmental conditions
- Tailored dimensions, shapes, or features such as flanges, locking mechanisms, or captive designs
- Customized surface treatments or coatings for enhanced durability
Such precision manufacturing supports complex assemblies where standard nuts might not provide adequate strength, fit, or corrosion resistance.
See also: Top Occupational Therapy Techniques for Daily Living
Benefits of Partnering with a Custom Nut Manufacturer
1. Tailored Solutions for Complex Challenges
Custom nuts solve problems standard fasteners cannot. For example, in aerospace, fasteners must endure extreme temperatures and vibrations. A custom nut manufacturer can engineer nuts with special alloys and locking features that guarantee safety and performance.
2. Improved Assembly Efficiency
Customized nuts can incorporate features that simplify assembly or reduce the need for additional components—saving time and labor costs.
3. Enhanced Product Longevity
Selecting appropriate materials and coatings tailored to the operating environment minimizes corrosion and wear, extending product life cycles.
4. Compliance with Industry Standards
A reputable custom nut manufacturer will ensure nuts meet or exceed certifications and standards such as ISO, ASTM, or aerospace and automotive regulations.
5. Competitive Advantage
Offering products with specialized fasteners that meet unique specifications can differentiate your company in competitive markets.
The Manufacturing Process of Custom Nuts
Requirement Gathering and Design
The process begins with detailed consultation to understand the application, load requirements, environmental factors, and any regulatory standards. Using CAD software, engineers design nuts that meet these criteria.
Material Selection
Materials such as stainless steel, carbon steel, brass, titanium, or exotic alloys are selected based on mechanical strength, corrosion resistance, and cost considerations.
Production Techniques
- Cold Forging: For high-volume production of nuts with excellent mechanical properties.
- CNC Machining: Used for highly precise or complex designs where forging is not suitable.
- Thread Rolling or Cutting: Methods to create internal threads ensuring compatibility with bolts or screws.
Heat Treatment
Many custom nuts undergo heat treatment to achieve desired hardness and strength.
Surface Treatment
Coatings such as zinc plating, galvanization, black oxide, or specialty finishes protect against corrosion and wear.
Quality Assurance
Strict inspections including dimensional accuracy, thread conformity, tensile strength, and surface integrity checks ensure compliance with specifications.
Packaging and Delivery
Proper packaging protects nuts from damage and contamination during transport and storage.
Choosing the Right Custom Nut Manufacturer: Key Considerations
1. Industry Experience and Expertise
Manufacturers with proven experience in your industry can better understand and meet specific requirements.
2. Quality Certifications
Look for ISO 9001, TS16949 (automotive), AS9100 (aerospace), or other relevant certifications.
3. Customization Capability
Assess whether the manufacturer can handle your required volume, complexity, and material demands.
4. Technology and Equipment
Modern machinery such as CNC machines, advanced forging presses, and automated inspection systems are indicators of manufacturing capability.
5. Customer Service and Communication
Transparent communication, timely updates, and technical support are essential for a successful partnership.
6. Lead Times and Logistics
Reliable delivery schedules and flexibility in order quantities prevent production delays.
7. Cost Competitiveness
Balance pricing with quality and service to ensure overall value.
Industries That Rely on Custom Nut Manufacturers
- Aerospace: Requires high-strength, lightweight, corrosion-resistant nuts that can endure extreme environments.
- Automotive: Custom nuts designed for engine components, suspension, and safety systems.
- Electronics: Miniature nuts with precise tolerances for delicate assemblies.
- Medical Devices: Biocompatible nuts used in surgical instruments and implants.
- Construction: Heavy-duty nuts with superior corrosion resistance for structural applications.
Emerging Trends in Custom Nut Manufacturing
Smart Fastening Solutions
Some manufacturers are integrating sensor technology into nuts to monitor torque, vibration, or stress in real time, improving maintenance and safety.
Additive Manufacturing
3D printing enables rapid prototyping and production of complex nut designs, speeding up development cycles.
Sustainable Practices
Eco-friendly materials and processes are gaining traction to reduce environmental impact.
Industry 4.0 Integration
Digital factories use IoT and AI to enhance quality control, reduce waste, and improve production efficiency.
Case Study: Custom Nut Manufacturer Enables Innovation in Renewable Energy
A wind turbine company needed nuts capable of withstanding offshore conditions with high salinity and constant vibrations. Partnering with a custom nut manufacturer, they developed:
- Nuts made of duplex stainless steel with superior corrosion resistance
- Integrated locking features to prevent loosening during operation
- Customized thread designs to simplify installation and removal during maintenance
This collaboration improved turbine reliability, reduced maintenance frequency, and extended operational lifespan.
Conclusion
Selecting the right custom nut manufacturer is a strategic decision that can greatly influence the success, safety, and longevity of your products. Custom nuts provide the flexibility and performance needed in today’s demanding industrial applications, offering tailored solutions where standard fasteners fall short.
By partnering with a manufacturer that combines advanced technology, material expertise, quality assurance, and responsive service, businesses can achieve superior assembly integrity and gain a competitive advantage in their markets.